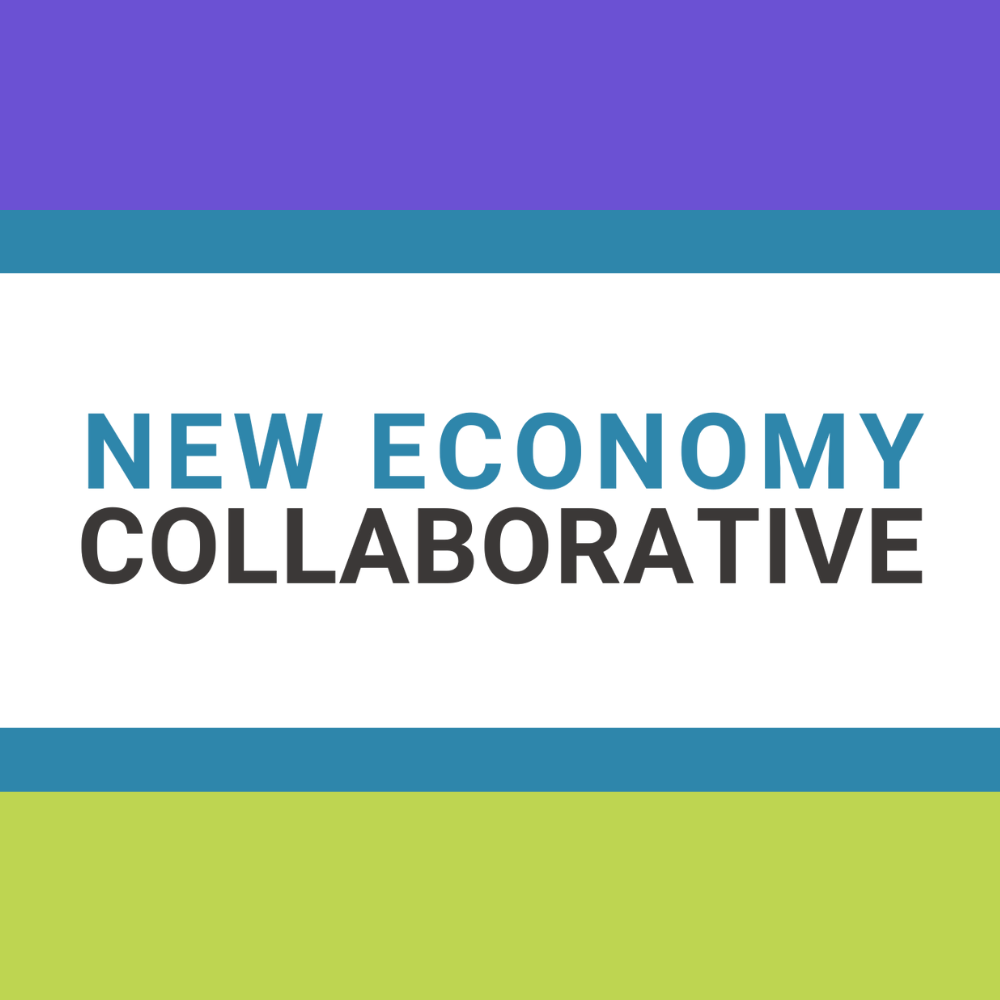
The New Economy Collaborative of Southwestern Pennsylvania announced a $62.7 million Build Back Better grant toward workforce development in Southwestern Pennsylvania. Follow Technical.ly’s coverage of the 11-county project here.
Most of Andrew Orr’s life has been dedicated to the growth and success of Penna Flame, the flame-hardening manufacturing company his grandfather started in 1968.
In middle school, Orr cleaned offices, shoveled rocks and painted pipes for the family business. He was later trained in flame hardening, a process of heating and cooling metal to make it more durable, while still in high school. Then, Orr continued to develop his knowledge of the business in college, working in Beaver County-based Penna Flame’s shop during breaks from studying for his bachelor’s degree in business management from Penn State.
Since graduating from college in 2009, Orr, now 38 years old, held several roles within his family’s company, including safety and quality control manager, as well as positions in sales and customer service.
Today, he’s vice president of the company, working alongside his father James Orr, the president of Penna Flame, to develop strategies that will help the family business succeed far into the future.
He still wears multiple hats, balancing his leadership role with active involvement in sales, HR and IT for the company, as well as being a board member for the Metal Treating Institute and the Southwest Corner Workforce Development Board.
However, one of his primary responsibilities is identifying and implementing new technologies and monitoring the company’s performance.
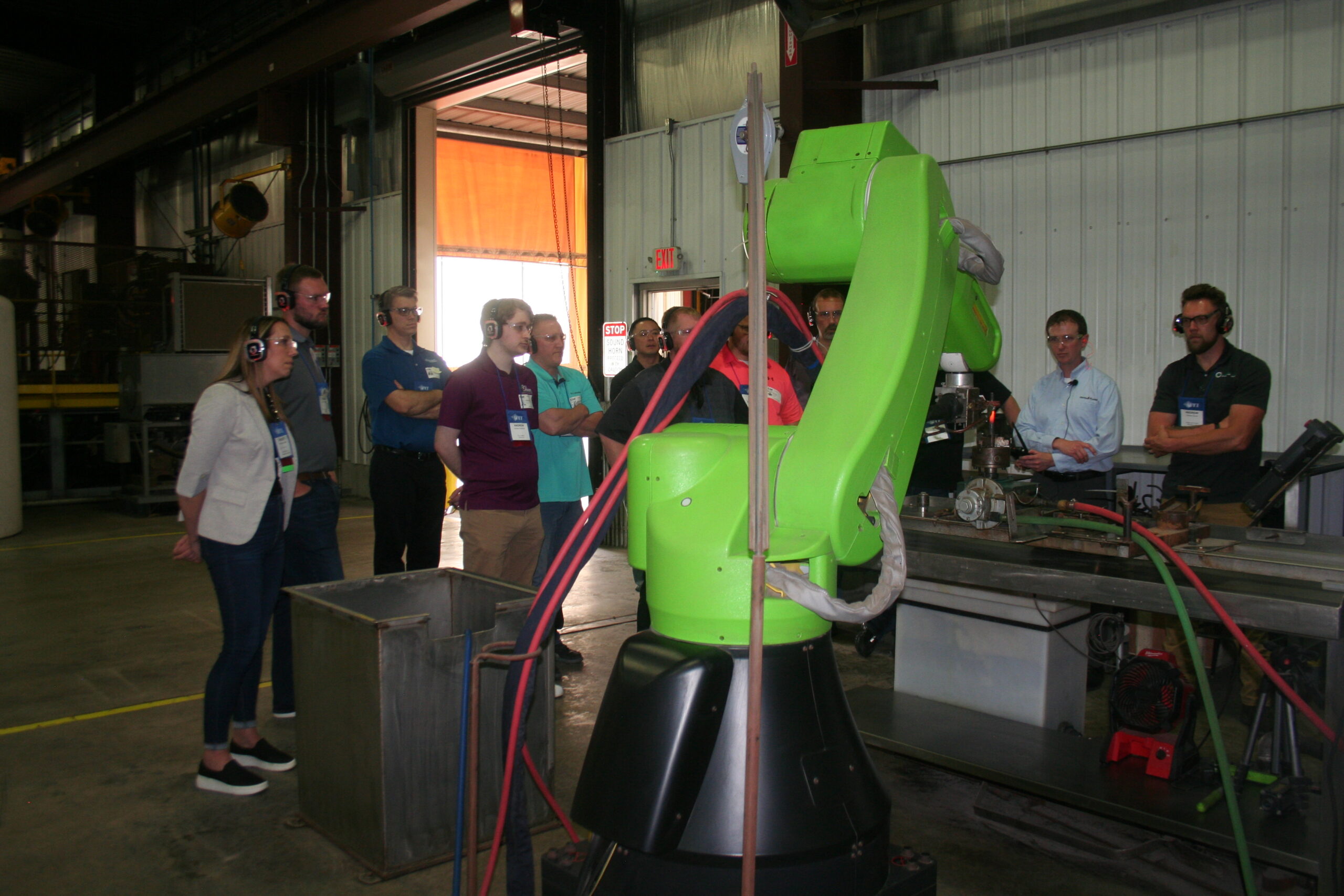
The manufacturer specializes in developing products like crane wheels, which are often designed to support and guide the movement of cranes along track or rail systems. Their products are also used in high-profile venues, including the Arizona Cardinals and Las Vegas Raiders stadiums, where these wheels help roll the field in and out of the stadiums.
Penna Flame recently worked with the Advanced Robotics for Manufacturing (ARM) Institute, which supports small and medium-sized manufacturers through its Robotics Manufacturing Hub program. Funded by the New Economy Collaborative’s $62.7 million from the Build Back Better Regional Challenge grant, the program offers free evaluation, prototyping and testing for robotics solutions.
Before joining the hub’s cohort, Penna Flame employees were still manually lifting and packing cast parts that weighed 30 pounds or more because the manufacturer’s robot needed further customization to undertake packing tasks. Now, the company has a proof-of-concept for a system that involves less manual labor, which they are working to install.
In this edition of Technical.ly’s How I Got Here series, Orr discusses how the manufacturing landscape has changed since the founding of the company and how other small manufacturers can take advantage of programs and new technologies.
This Q&A has been edited for length and clarity.
What is unique about working for a family business?
There’s a sense of pride working for a family business. My grandfather started this company with not a whole lot but a shovel in his hand for the groundbreaking back in 1968. My dad was involved with the company by the mid-to-late 1970s and he was instantly hooked. He really grew the company to what it is today.
I’ve always been asked the question by people who know my dad: What is it like trying to fill your father’s shoes? My answer to that is I’m trying to fill my own shoes, but at the same time, in the back of my mind, there are some high expectations. There is pressure and a never-ending list of things to do.
How have economic changes in the region altered the industry?
When my grandfather founded this business it was between Cleveland and Pittsburgh, with a focus on the Youngstown area. Youngstown has fallen off significantly from an industrial standpoint. There are still many small businesses around Pittsburgh focused on supplying industry, whether that be mining or steel making, though.
The expectation used to be, during my grandfather’s time, that there’s this part that needs to be hardened and given back as quickly as possible. Now it’s paperwork all over the place. It’s interesting to see that we can go from working with a mom-and-pop shop that’s just down the street to now working with multinational corporations as well.
This region has really become the industrial wheelhouse for the country. We have quite a few customers now who are involved in making products that would go into material handling, like overhead cranes in a steel mill or some railroad items.
How has the rise of advanced manufacturing and robotics impacted your business?
There’s been quite a few changes over the years. We started in 2007 with a collaboration with Robert Morris University. They purchased 50% of a robotic arm and we purchased the other 50%. They taught a class with the arm for a semester and then the robotic arm became ours, and we hired someone from that class. It was a great collaborative effort and that’s how we got started with robotics, although we didn’t really know how we could use it yet.
It’s gone from barely knowing anything to now processing parts that we would never have if we didn’t have that technology.
If it can save one back injury, that would pretty much pay for the whole system.
Andrew Orr, VP at penna flame
Since then, we’ve added two more flame-hardening robots, one collaborative robot for induction hardening and, in two weeks, we’re expecting to receive our newest robot for picking up packing parts.
Robotics offers us the ability to control the process, repeat it and make it safer for employees. For example, the new picking and packing robot, we’re going to put that in place to take away the least favorite job that anyone here has to do and allow them to do something more productive.
We luckily haven’t had to deal with any back injuries from packing jobs but this robot is potentially going to save some backs. If it can save one back injury, that would pretty much pay for the whole system.
How did working with the Robotics Manufacturing Hub impact Penna Flame?
We got started working with them through Catalyst Connection. It’s hard to implement new technology and buy new robots without help from local organizations like Catalyst Connection and the ARM Institute.
The ARM Institute was nice enough to accept our situation and what we wanted to do. They thought it was a great idea and then they helped us de-risk the process.
Originally, just asking ourselves the questions needed to implement this new technology, we couldn’t see the big picture and the ARM Institute was able to show us that big picture and help us work through things step by step to get to the final result.
There’s also been some grant money available that really has helped small businesses like ours be able to actually implement the technology.
What advice would you give small manufacturers looking to succeed in this economy?
I got involved with the Workforce Development Board, which works throughout this Southwest corner region. If you’re looking to train individuals to use this new technology, they have the funds to get that done. They can do incumbent worker training to upscale your current workforce. They can also help with initial training costs and onboarding.
Small manufacturers should reach out to companies like Catalyst Connection that are out there. They’re there to help and they’re very friendly people that want to point you in the right direction. Getting in touch with them and starting a conversation can’t hurt.
The worst-case scenario is you end up right where you started, but I find that to be very unlikely.
Join our growing Slack community
Join 5,000 tech professionals and entrepreneurs in our community Slack today!
Donate to the Journalism Fund
Your support powers our independent journalism. Unlike most business-media outlets, we don’t have a paywall. Instead, we count on your personal and organizational contributions.

Philly’s Venture Cafe, the once-popular University City meetup, shuts down after 6 years

How Duolingo’s social media team built a viral marketing strategy

Abridge CEO says ‘hypergrowth’ is why it’s moving to hire in San Francisco, sparking talent debate in Pittsburgh ecosystem
