A Baltimore company has a new product that’s designed to put cells in their natural habitat during tests.
BioPapers, recently launched by nanofiber manufacturing company DiPole Materials, can be used by pharmaceutical companies during drug discovery, as well as tissue engineering and 3D bioprinting, said DiPole CEO Ken Malone.
The product is designed to made of very thin fibers of the protein gelatin. The nanofibers can be treated to create a scaffold that is similar to the environment in which a cell grows inside the body. This makes it distinct from synthetic environments like cell culture plates, Malone said.
“Our customers needed a standardized scaffold that made cells behave like they do inside the human body. They were frustrated that the only available scaffolds were of synthetic materials which caused cells to misbehave,” DiPole cofounder Scott Gaboury said.
So far, Malone said the company has found the most traction from big pharmaceutical companies, which would use the BioPapers to screen hundreds and thousands of drugs. The sheets sold to the pharma companies look like this:

(Photo courtesy DiPole Materials)
“Each well has a piece of BioPaper in it,” Malone said. “Our pharma customers grow cells on the paper, then put drops of various drugs onto those cells and determine toxicity or efficacy of the drugs from it.”
Other applications could include tissue engineering for growth of stem cells. It could also be used as the “paper” that is used during 3D bioprinting, Malone said.
BioPapers are made using a process called electrospinning, which draws an electric charge to create fibers. The machinery is the same DiPole used to produce a piezoelectric yarn that the company is also currently developing and could be used in smart garments. Here’s what the nanofibers look like under a microscope:
Malone said the team discovered work on BioPapers at the U.S. Naval Research Laboratory in D.C., and later licensed the technology. It received funding through TEDCO’s Technology Validation Program to develop the concept, and investment from the Abell Foundation helped get it to launch, Malone said.
Now, production is located within Harbor Designs and Manufacturing space at the Wicomico building in Pigtown. Harbor, which performs contract manufacturing for various companies including medical device makers, has offered some Baltimore startups the option to colocate within the recently-expanded facility.
Malone said there’s plenty of capacity to manufacture the volumes required over the first couple years of production.
Before you go...
To keep our site paywall-free, we’re launching a campaign to raise $25,000 by the end of the year. We believe information about entrepreneurs and tech should be accessible to everyone and your support helps make that happen, because journalism costs money.
Can we count on you? Your contribution to the Technical.ly Journalism Fund is tax-deductible.
Join our growing Slack community
Join 5,000 tech professionals and entrepreneurs in our community Slack today!
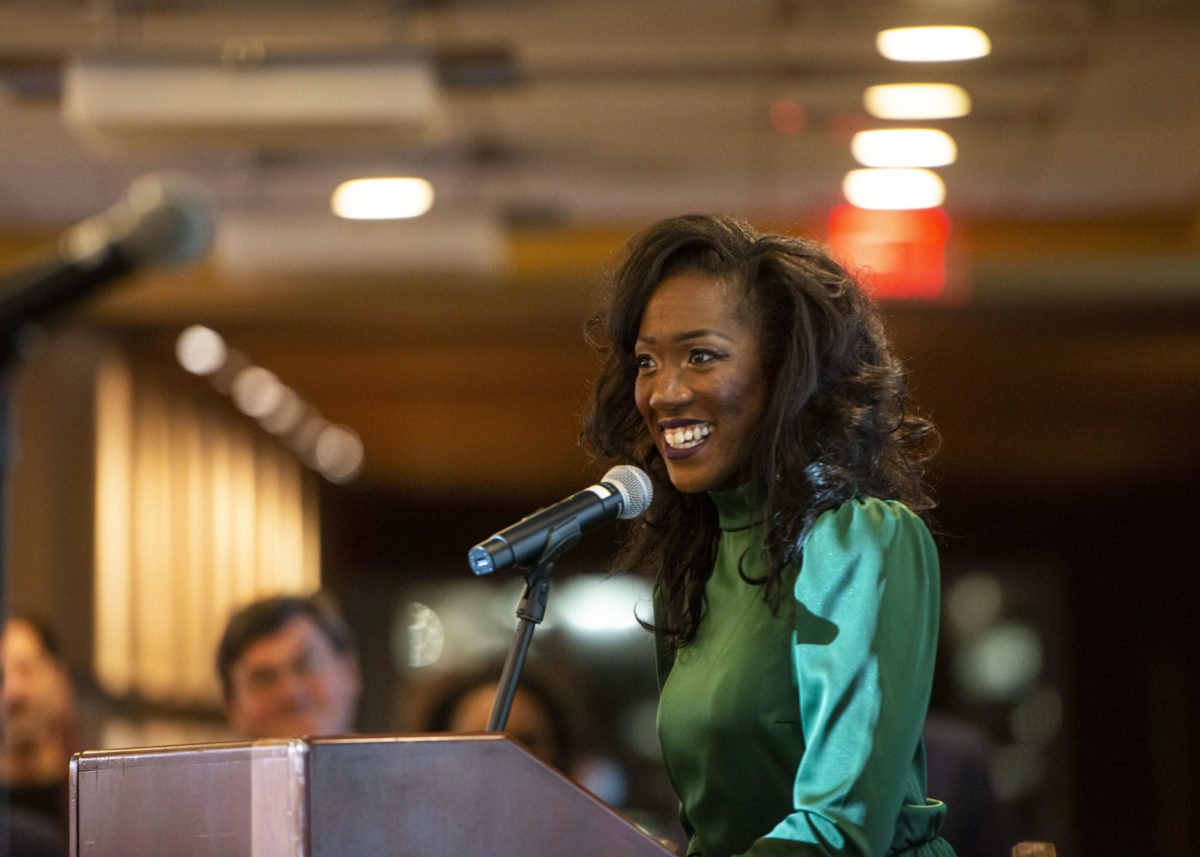
Looking for startup funding? Here are 28 terms to know

Congress votes to reauthorize the EDA, marking a historic bipartisan effort to invest in innovation and job creation

Looking for a job? This strategy turns NotebookLM into your personal hiring coach
