In the spirit of robotics advancement, a Pittsburgh workforce development organization will provide millions in funding to new academic and industry partner projects.
The Advanced Robotics for Manufacturing Institute announced last month that it had selected eight new robotics technology projects to fund, focused on addressing the Department of Defense’s Modernization Priorities as they pertain to manufacturing. The news came on the tails of President Biden’s visit to Mill 19 at Hazelwood Green, which houses the ARM Institute along with Carnegie Mellon University’s Manufacturing Futures Institute and Catalyst Connections.
Across the eight projects, the ARM Institute will provide $8 million in funding, adding on to its previous investments in over 90 robotics technology and workforce development projects.
“These projects represent the expertise and commitment of 27 unique member organizations to tackle key manufacturing modernization challenges for the defense and commercial sectors requiring robotic technologies,” said Charles Brandt, VP of technical initiatives at the ARM Institute, in a statement.
The eight projects feature partnerships across academia and industry, including a collaboration between manufacturing and engineering tech company Siemens and Carnegie Mellon University, GelSight Inc., ATI Specailty Alloys and Components and Boeing — the only project with Pittsburgh-based partners.
Siemens will act as a lead for the project, bringing the partners together to develop a visual tactile inspection system that can identify surface defects or inconsistencies in spacecraft components or airplane fuselages. In the long term, the hope is that the development of these tools will improve aviation maintenance operations by improving the inspection, as a description of the project said. And even beyond the aviation industry, the combined use of AI and robotics in developing the visual tactile inspection system could hold benefits for inspection processes across other industries.
The other seven projects are listed below, with provided descriptions. Check out the full descriptions via the ARM Institute.
AI Robot Programming Assistance
- University of Memphis
- Partners: READY Robotics, FedEx, DeepHow
- There are technologies that can now dramatically reduce the knowledge necessary to program and install a robot, using no-code methods that make robotic programming accessible to those on the factory floor. However, there is still the limitation of process automation knowledge that can bottleneck or be a detriment to a successful robotic installation. This project aims to create an assistance system which can act as a stopgap for this lack of expertise by providing suggestions and corrections during robot task programming.
Optimized Robot Motion Program for Tracking Complex Geometric Paths
- Rensselaer Polytechnic Institute
- Partners: GE Research, Southwest Research Institute, Wason Technology
- This project aims to autonomously create a high-speed and high-precision curvilinear robot tool trajectory on a complex curved geometry using industrial robots with redundant degrees of freedom, to reduce or eliminate the need for manual tuning often required today.
Autonomous Robotic Metal Forming
- Ohio State University
- Partners: Yaskawa, CapSen Robotics
- The project team will address the challenge of low volume, high mix production of complex metallic components.
Uniform Work Robotic Sanding with Intra-stage Inspection
- GKN Aerospace
- Partners: National Institute of Aerospace Research, GrayMatter Robotics, University of Washington, EWI
- Past ARM Institute projects on automated surface-finishing worked on path-planning, uniform finishing, and automated inspection. The project team will combine the outputs from these past projects to create an effective sanding and polishing technology that benefits multiple industries.
High Precision Adaptive Machining for High Temperature Materials
- GE Research
- Partners: GrayMatter Robotics, FANUC
- The project team will focus on enabling high-precision adaptive machining of complex cooling circuits in high temperature materials through the development of an open architecture framework that integrates sensor data and automatically adjusts tool paths and process parameters to achieve an optimal solution for laser drilling.
Ceramic Matrix Composites Pick, Place, and Form Automation
- Boeing
- Partners: University of Southern California, 3M Company
- The project team plans to develop automated trajectory planning for forming fabric-based prepregs to contours, automated in-process inspection for un-compacted areas and automated generation of rework tool paths, and self-corrective robotic recovery for prepreg backing film removal failures.
Safe Robotic Handling of Energetic Materials
- Rensselaer Polytechnic Institute
- Partners: Schlumberger, Interface Technologies, FANUC
- The project team aims to develop fundamental technologies for robotic handling of energetic materials.
Before you go...
Please consider supporting Technical.ly to keep our independent journalism strong. Unlike most business-focused media outlets, we don’t have a paywall. Instead, we count on your personal and organizational support.
Join our growing Slack community
Join 5,000 tech professionals and entrepreneurs in our community Slack today!
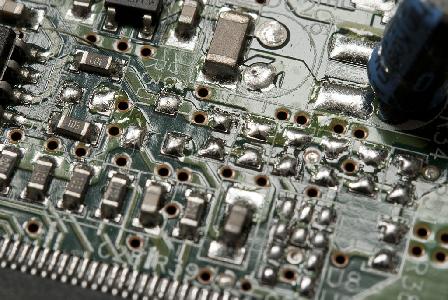
Millions of dollars pour into semiconductor manufacturing in Southwestern PA
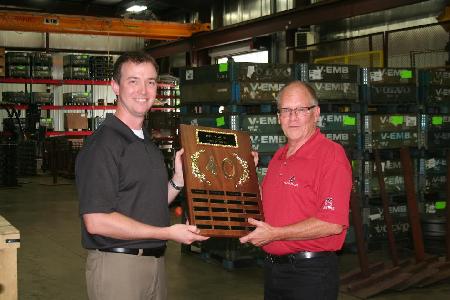
How robots are transforming an old-school Pennsylvania manufacturing firm — and reducing risk of injury
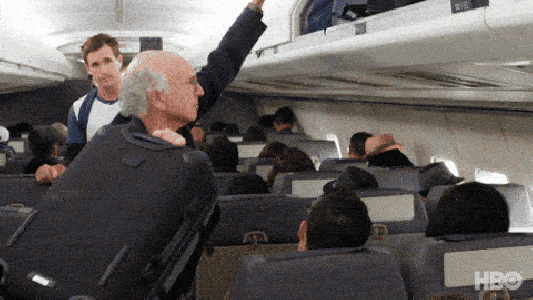
This Week in Jobs: Travel far in your career with these 26 open tech roles
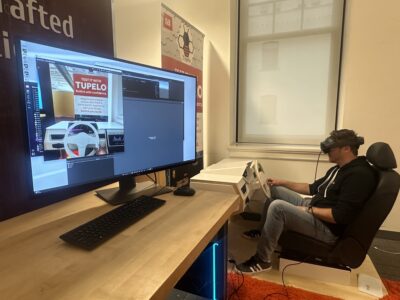