
This article appears in a series on manufacturing in Delaware and is underwritten by Delaware Prosperity Partnership. It was independently reported and not reviewed by this partner before publication.
In Delaware, manufacturing is a $5 billion industry, with a whopping 94% of the state’s global exports coming out of it.
When you think of manufacturing, you might think of factories that produce consumer products like cars. But Delaware has always been more of an industrial manufacturing state, with its top five sectors, according to the Delaware Prosperity Partnership, being pharmaceutical and medicine; agricultural chemical; control instruments; basic chemical; and other general-purpose machinery.
Allied Precision Contract Manufacturing, based in Middletown, falls into the fifth category — the company makes “widgets,” often machine parts needed to build and assemble products.
John Lees, the owner of Allied Precision, started the beginnings of the company in his garage in 1991. He grew up in the Newark area and attended school in the New Castle County Vo-Tech School District.
“I knew I wanted to pursue a career in this business at a very early age,” Lees said. “Even as a little kid, I just had the desire to build stuff. My father helped in that regard — he was a machinist and engineer in his day, so I guess you could say it’s in my blood.”
In 1995, Allied Precision was formally founded, with a small shop in Newark. By the early 2000s, the company had outgrown the shop and Lees started looking for a new location.
“In the early 2000s, Middletown was booming,” he said, “so we decided to come down and set up shop down here. It turned out to be a wise thing to do.”
The facility has 15 computerized machining centers, all programmed and operated by a skilled team of 15 employees, who work in two shifts. That means there are about seven or eight people working in the large space at a time — a plus during the COVID-19 pandemic, especially since contract manufacturing companies are considered essential businesses.
“The client base that we have still needed parts during the pandemic,” he said. Those include parts needed in the medical, transportation and agriculture industries. “We ended up getting busier through the shutdown.”
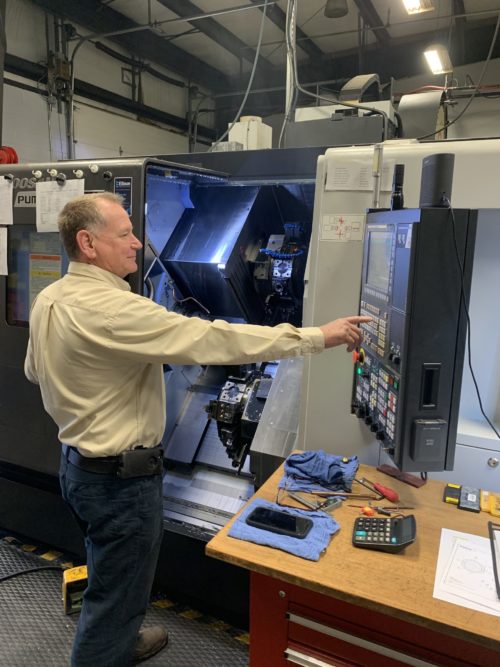
One of Allied Precision’s machining centers. (Courtesy photo)
In the spring, when fears of a potential ventilator shortage were at their height, Allied Precision was contracted to make component parts for ventilators.
“That’s just one of the many needs that were and still are out there,” Lees said.
While the company manufactures parts for virtually every facet of industry in the world, it does have a niche in the defense industry, manufacturing parts for final products they often aren’t privy to.
“Our orders can range from one to two parts to 20,000 to 30,000 parts,” Lees said. “We’ve got different machines that lend themselves to processing parts very efficiently.”
Manufacturing is the backbone of what keeps the country going, and we're proud to be a part of that.
A high level of skill is required, which young people considering manufacturing careers can begin to develop at vo-tech high schools and via some Delaware Pathways programs like engineering.
Apprenticeships are one way to grow from high school to a career in manufacturing.
“I was fortunate as a young fellow to get a state-sponsored apprenticeship under my belt at a very high-end shop across town,” he said. “There was a number of journeymen that took me under their wings to teach me the trade, and it’s turned out to be a very valuable asset.”
In that spirit, Allied Precision sponsors youth coming out of their last year of high school to join for summertime positions.
“We expose them to different operations in the shop, just to get their feet wet so it can prepare them for engineering and/or machining occupations down the road.”
After nearly two decades based in Middletown, Lees says he’s seen an evolution that is still underway.
“Twenty years ago, Middletown was quite rural, but it’s grown leaps and bounds business-wise,” he said. “It’s been growing steady — probably too fast for its own good. It’s just convenient, and now with the bypass going through it’s even more convenient to get to Philly and Baltimore and everywhere. It’s worked out well for us.”
By way of reminiscing on the time that’s passed, some of Lees’ favorite parts wind up in a display case at the facility.
“I’ve got a whole showcase here, full of a large variety of parts,” he said. “I often say that there’s a story with every one of the parts in the case. It’s a culmination of 25-plus years of making parts for different folks and different companies around the world.
“Manufacturing is the backbone of what keeps the country going, and we’re proud to be a part of that.”
Join the conversation!
Find news, events, jobs and people who share your interests on Technical.ly's open community Slack
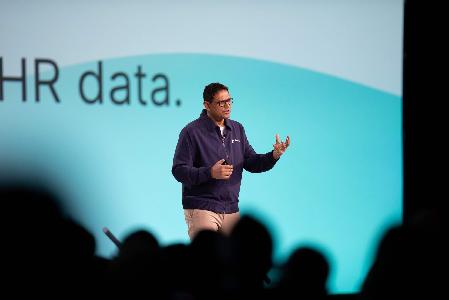
Is AI really something new — or just the next big technology platform?
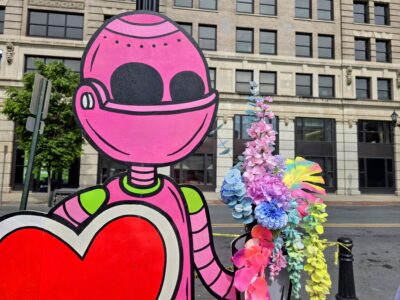
Meet the artist behind the robots you’re seeing take over Wilmington
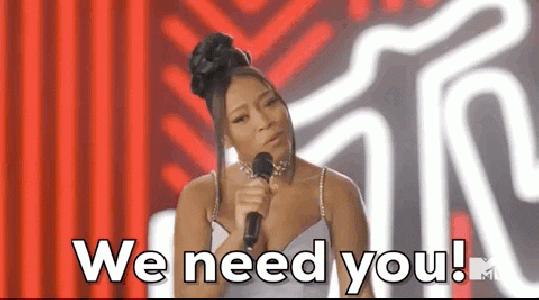
This Week in Jobs: Get out there with 22 new job opportunities available to you!
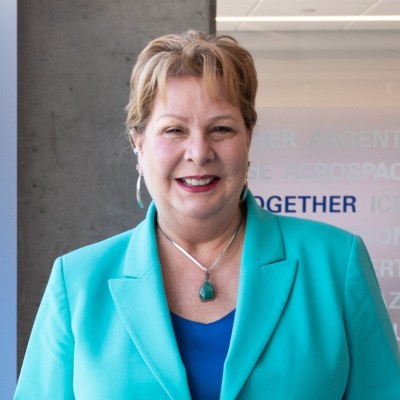